Rotary encoder manufacturer in China
- Low MOQ, both hollow shaft and solid encoders available
- Supporting OEM and ODM
- All kinds of certificates availble, CE, RoHS, FCC, ISO9001
- Two years long warranty time
Hollow shaft incremental rotary encoder
We appreciate the hard work of our workers and engineers in manufacturing and developing hollow shaft encoders. Lorentzzi is proud to be a leading encoder manufacturer in China. This is our most popular incremental encoder, characterized by its ease of installation, high accuracy, and long durability. Lorentzzi offers a wide variety of hollow shaft encoders, ranging from miniature encoders to large diameter encoders. Furthermore, in terms of resolution, we offer both high-resolution rotary encoders and low-resolution, cost-effective encoders.
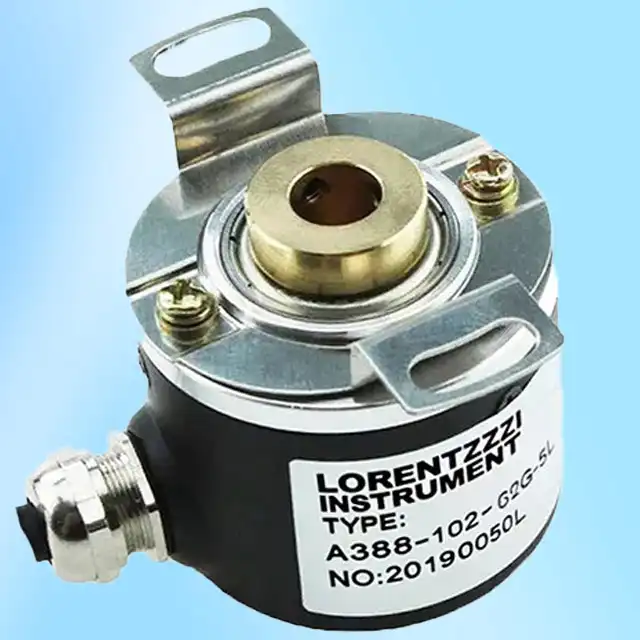
Solid shaft incremental rotary encoder
Solid-shaft encoders have a slightly narrower range of applications than hollow-shaft encoders. They are more suitable for use with encoder couplings to measure motor speed, displacement, and acceleration. Lorentzzi manufactures high-quality encoders with resolutions ranging from 100 ppr to 5000 ppr, with higher resolutions resulting in higher accuracy. Furthermore, our solid-shaft encoders are available in outer diameters of 25 mm, 30 mm, 38 mm, 50 mm, 58 mm, 70 mm, and 78 mm. Custom sizes are also available. Click the button below to learn more!
Our products
-
Blind type hollow shaft incremental encoder, Outer diameter 40 mm,...
-
Resolution is programmable according to different applications, Easy to use...
-
External diameter can be 38mm, 40mm, 50mm and 58mm etc.,...
-
OD 100 mm large bore, Hollow shaft diameter 35 mm...
-
Outer diameter range: 38 mm to a maximum of 120...
-
Output 100 ppr, Line driver output, strong anti-interference, Various external...
-
Outer diameter 25 mm, shaft diameter 4 mm, Maximum resolution...
-
OD 58 mm, shaft 8 mm, 2500 pulses per revolution,...
-
Various shaft diameters available 1000 pulses per revolution, A B...
-
Available in various outer and shaft diameters, 5400 PPR high...
-
External diameter 50 mm, Shaft diameter 6 mm or 8...
Why Choose Lorentzzi to be your supplier?
Outstanding product quality
Lorentzzi always puts product quality first, and we strictly select the highest quality parts so that you can sell or use them without any worries.
Fast delivery time
Our experienced workers and sales team are highly efficient, we keep our stock at a level, which makes our delivery time very fast and efficient.
100% aging test
Every optical rotary encoder needs to go through a full-time aging test before leaving the factory. We spend more time and customers spend less time after-sales.
Incremental rotary encoder applications
Pharmaceutical factory
Printing industry
Medicical equipment
Cement factory
Textile factory
Elevator speed control
The Ultimate Guide to Incremental Rotary Encoders
Introduction
In today’s industrial control and our daily life, incremental encoders play a very important role. The most common examples are the height, speed, and door opening control of elevators.
This article mainly talks about what an incremental encoder is, how an incremental encoder works, application range, advantages and disadvantages, and the comparison between an incremental encoder and an absolute encoder, etc.
What is an Incremental Rotary Encoder?
An incremental encoder is a device that measures a physical status of rotation or linear motion.. It can convert the displacement, acceleration, and speed of rotating objects that are not easy to measure into measurable digital signals.
In addition, there is a more powerful encoder than an incremental encoder, which is an absolute encoder. The absolute encoder output is a Gray code, so the output is different for each position. Another advantage brought by this characteristic is that when the power fails, the absolute encoder output can still read position information.
Incremental encoders are mainly used to measure displacement, speed and acceleration, while absolute encoders are mainly used to measure angle.
How Does It Work?
The incremental encoder is mainly composed of three parts: a code disc, a photosensitive element and a counting circuit. Its principle is based on the photoelectric effect and the geometric structure of the disc.
The encoder code disc is etched with different number of slits according to different resolutions, the higher the resolution, the more the number of slits. The code disc is fixed to the bearing. During the rotation, the photoelectric transmitter generates a pulse on the receiver each time it passes through a gap. By calculating the number, direction, frequency, etc. of the pulses in the sequence, physical parameters such as the moving direction, distance, and speed of the object can be calculated.
Incremental encoder signal output includes totem pole(also named complementary output), open collector(NPN, PNP), voltage output, line driver.
Line driver encoder, which has differential outputs, is suitable for long distance signal transmission. The reason is it uses the phase and its reversing phase value difference to calculate displacement. Thus, it has a strong anti-interference ability.
The output phase can be divided into:
A or B single-phase, there is only a pair of photocouplers inside, which can only generate a pulse sequence. It is mainly used for speed measurement and cannot judge the forward and reverse directions.
There are two phases A and B, and the difference between phase A and phase B is 90°, which is called AB quadrature, which is used for forward and reverse counting, judgment of forward and reverse and speed measurement.
A, B, Z three-phase, Z phase is the zero pulse signal, used to determine the zero position, so the encoder with this output is used for position measurement with reference position correction.
A, A-, B, B-, Z, Z-six phases, due to the connection with a symmetrical negative signal, the electromagnetic field contributed by the current to the cable is 0, the attenuation is the smallest, the anti-interference is the best, and it can be transmitted over a long distance.
Why Can ABZ Encoder Be Used to Detect Motor Forwarding and Reversing?
As shown in the figure below, if the motor is forwarding the AB output signal is 10, 11, 01, 00, 10, 11, 01, 00, 10, 11, if the motor is running in reverse, the AB output signal is 11, 10, 00, 01, 11 , 10, 00, 01, 11, according to the output of this series of signals, it can be distinguished whether the motor is rotating forward or reverse.
Applications of Incremental Encoders
Heavy-Duty Environments: Incremental encoders play a vital role in heavy-duty environments such as mining, construction, and heavy machinery. They are used to monitor and control the position, speed and direction of various components, ensuring precise and reliable operation even under harsh conditions.
Industrial Applications: Incremental encoders have a wide variety of applications in industrial environments, including manufacturing, automation, and robotics. They are used to provide feedback for motion control systems, motor control, positioning and synchronization of industrial machinery. Encoders help optimize production processes, increase efficiency and ensure precise positioning and control.
Light Duty/Servo Applications: Encoders are critical in light duty and servo applications that require precise positioning and control. These include robots, CNC machine tools, printing equipment, medical equipment and small automation systems. Encoders provide accurate feedback to ensure precise positioning, speed control and smooth operation in these applications.
Advantages and Limitations
The advantages of incremental encoders are simple structure, long mechanical life, high reliability, low cost, and simple installation. The disadvantages are that there is zero point cumulative error, poor anti-interference, power-off memory is required when the receiving equipment is stopped, zero or reference position should be found when starting up, etc. These problems can be solved by using an absolute encoder.
Incremental Encoders vs. Absolute Encoder
Incremental encoders differ from absolute encoders in the following ways:
- The code disc is different. The gap between the code disc of the incremental encoder is evenly distributed. The code disc of the absolute encoder is divided into many slots of different sizes.
- Incremental encoders do not have a power-off memory function because their code discs are evenly distributed. On the contrary, absolute encoders have different gray codes for each position of the code disc, so they have a power-off memory function.
- Incremental encoders have no range limitation. The counter can count forward all the time, while absolute encoders have range limitations. For example, single-turn absolute value encoders only have a 360-degree measurement range, and multi-turn absolute value encoders have only 360-degree measurement range. It depends on the number of gear boxes, how many turns are a cycle, for example, 4096 turns, and if it exceeds 4096 turns, it will return to the 0 point cycle.
- Incremental encoders are cheaper because of their simpler production process than absolute encoders.
- The output signals are different. The incremental encoder outputs a pulse signal, while the absolute encoder outputs a set of binary values.
Key Features to Consider
The IP grades of conventional incremental encoders are IP65 and IP67. This waterproof grade determines the need to pay attention to waterproof and rainproof during use. The solution can be to use an encoder with a protection grade of IP68.
Another point that needs to be considered is the impact of high temperature on the encoder. The material of the encoder disc is glass, metal, film, and resin. If the encoder disc is made of film or resin, the encoder disc will be deformed at high temperature, resulting in output. inaccurate phenomenon.
In addition, be careful not to knock the encoder during use, because if the code disc is made of glass, knocking may cause the code disc to break and cause product damage.
For more points to pay attention to, please check this article: https://lorentzzi.com/encoder-problems-with-solutions-the-ultimate-guide/
Installation and Maintenance
- Check the mechanical part of the encoder regularly, usually once a month. The content of the inspection work is mainly to check the mechanical connection points to see if there is any misalignment.
- The use of the encoder needs to be used together with the controller, electric control system and other equipment. These equipment have high power and different operation methods, so the maintenance and maintenance work should be performed by professionals.
- The encoder is a precision instrument, and the electronic control equipment in it cannot be adjusted at will, especially the interlock device. On the one hand, it is to ensure the normal use of the encoder, and on the other hand, it is to ensure the use of personnel.
- When the encoder fails, non-professionals should not tamper with it without authorization, and should notify the maintenance personnel to find out the cause of the failure and repair it in time.
FAQs
If the requirements for position and displacement control are relatively high, you can choose an absolute encoder. The accuracy of an absolute encoder is much higher than that of an incremental encoder, but it should be noted that the absolute encoder has a limited range. In addition, if the power-off memory function is required, be sure to use an absolute encoder.
To check for an encoder issue, follow these steps:
- Check whether the wiring of the encoder is correct, wrong wiring will result in no output pulse.
- Check whether the power supply voltage is correct. The common working voltage is 5VDC, 8-30VDC. If the voltage is too high or too low, the encoder cannot work normally.
- Check whether the code disc of the encoder is deformed or broken. As mentioned above, the code disc made of glass is easy to break, and the code disc made of film and resin will deform under high temperature conditions and cause output errors.
- Remove excess dust and oil. Since the encoder needs to be used with a large machine, a large amount of dust and oil will be generated during the operation of the large machine, which will cause the encoder to fail to operate normally.
Correct installation, regular maintenance, and ensuring that the encoder is used under suitable temperature and humidity conditions can effectively prolong the service life of the encoder.
Conclusion
Incremental encoders are widely used in various industries, providing precise position, speed, and direction measurements. They are ideal for heavy-duty, industrial, and light-duty/servo applications. While incremental encoders have simple structures and low cost, they have limitations such as zero point cumulative error and poor anti-interference. Absolute encoders offer a power-off memory function and higher accuracy but have range limitations. To optimize the life and performance of rotary encoders, proper installation, regular maintenance, protection from high temperatures and impacts, and adherence to IP grades are crucial. Consulting professionals for troubleshooting and following recommended usage guidelines are also important.